While last-mile delivery is typically a small part of a product’s journey to the customer’s doorstep, it’s the only stage that directly shapes the customer experience. It has the power to either strengthen or damage your business reputation and can become the difference between a loyal customer and a dissatisfied one. Naturally, shippers strive to perfect their last-mile delivery, facing a number of challenges on their way. Today, we’ll focus on the most common ones, along with solutions to overcome them.
1. High Traffic Congestion
Traffic congestion, especially in densely populated areas, is a huge source of headaches for truck drivers. Delivery trucks face extended delays due to heavy traffic, particularly during peak hours, which, in turn, impacts delivery times and increases the risk of late deliveries. Frequent stops and starts in traffic also result in higher fuel consumption and vehicle wear, driving up operational costs for logistics companies.
To overcome this problem, many companies are turning to route optimization software. Modern real-time data tools and technologies allow dispatchers to select the most efficient routes, bypassing congested areas and minimizing delays. Another solution is implementing off-peak deliveries. This strategy involves scheduling deliveries during non-peak hours, such as early mornings or late evenings, reducing time spent in traffic and improving overall efficiency.
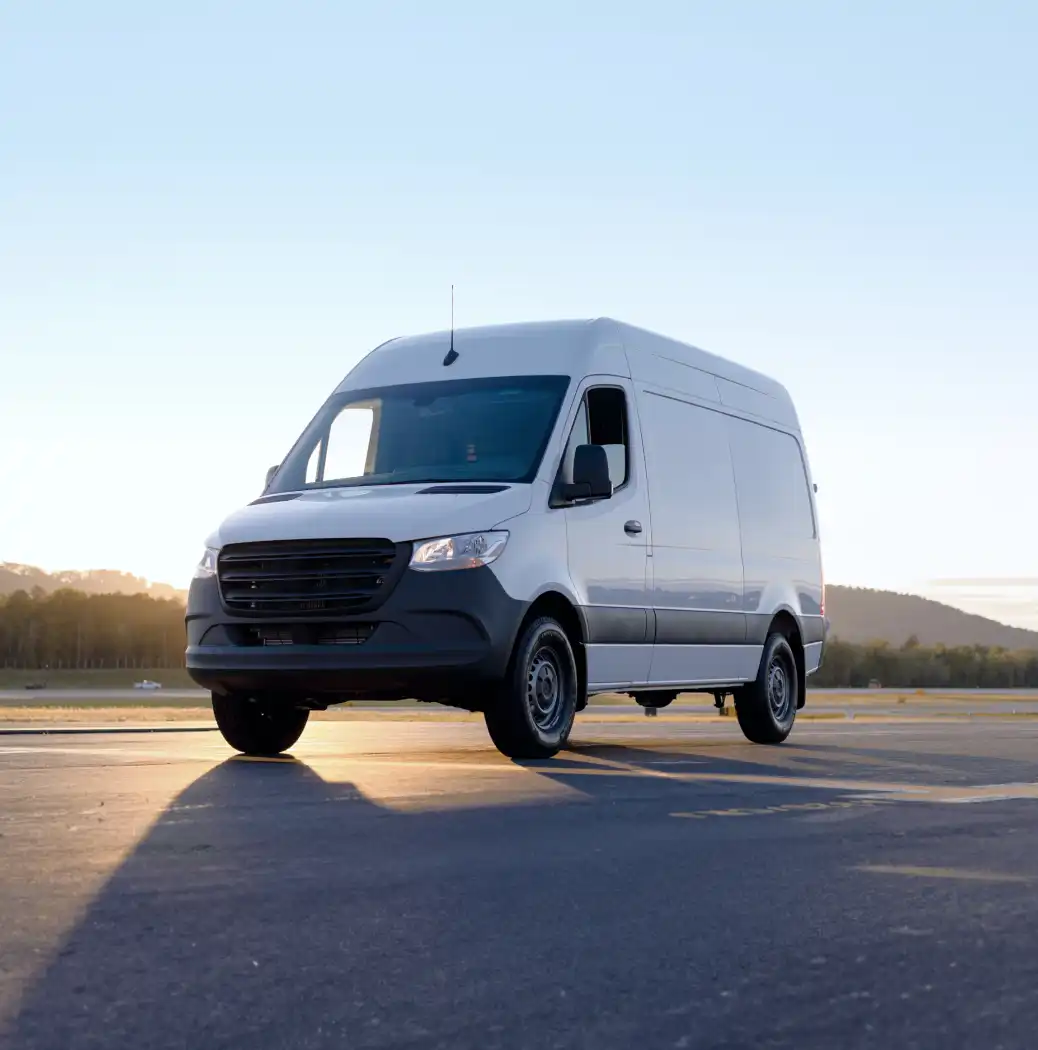
2. Limited Access in Urban Areas
Narrow urban streets present another significant challenge for last-mile delivery. Many cities have restrictions on delivery vehicles, especially in downtown cores where large trucks may be prohibited during certain hours or entirely. Add to this lack of parking and pedestrian-heavy zones, and you get nothing but complicated deliveries and delays.
An evident solution is to use smaller, more compact vehicles like cargo vans or box trucks for urban deliveries. These vehicles are better suited to maneuver through tight spaces and comply with urban restrictions. Some companies have also adopted micro-fulfillment centers located closer to their urban customers. These small-scale warehouses reduce the distance between the product and the customer, allowing faster and more flexible delivery options.
Another innovative solution is using drones or autonomous robots for deliveries in highly congested areas. While still in the experimental stages, these technologies could become viable options for overcoming the challenges of limited access in urban centers.
3. High Operational Costs
The cost of last-mile delivery can sometimes take the lion’s share of total shipping costs. Factors such as fuel prices, labor costs, and vehicle maintenance contribute to these expenses. Don’t forget about the increasing demand for faster, same-day, or next-day delivery that further puts a strain on profit margins.
To reduce operational costs, logistics companies invest in automation and technology. For instance, automated sorting systems in warehouses can speed up the process, reducing labor costs and improving efficiency. Different route optimization tools also helps reduce fuel consumption and vehicle wear by minimizing unnecessary driving.
Consolidating deliveries is also a good idea if you’re aimed at reducing operational expenses. Instead of making multiple individual stops, companies can group deliveries that are going to the same area, maximizing vehicle capacity and reducing the number of trips required.
4. Seasonal Demand Fluctuations
During peak seasons such as holidays, e-commerce spikes drastically, leading to overwhelming delivery volumes that strain logistics networks. Companies may struggle to meet delivery deadlines, and overworked delivery personnel could lead to mistakes or missed deliveries. The inconsistent demand across seasons further complicates workforce and vehicle management, as companies need to balance between underutilization in low seasons and being overwhelmed in high seasons.
The most efficient way to overcome this challenge is scalable logistics planning. Consider employing temporary workers or using third-party delivery services during peak seasons to meet increased demand without long-term resource commitments. Flexible warehouse space and outsourced fleet management can also help scale operations to match demand without the need for excessive capital investment.
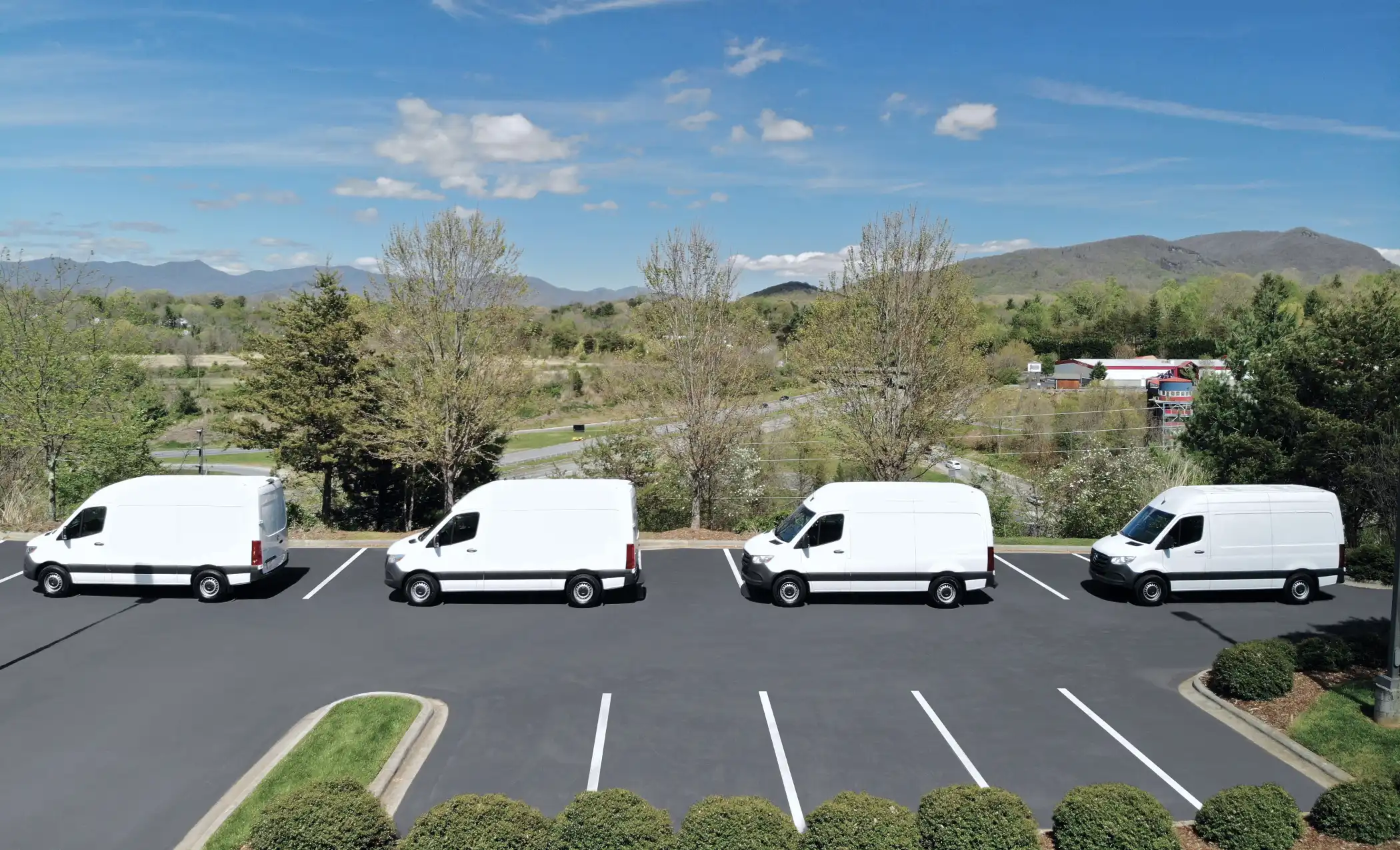
5. Unavailability of the Customer
Missed deliveries lead to reattempts, increasing costs and delaying other shipments. In some cases, customers may not even be aware of the delivery time, resulting in frustration for both the customer and the logistics provider. The issue also contributes to additional fuel consumption and time wastage, further impacting the efficiency of the supply chain.
To counter this problem, companies utilize real-time delivery tracking and notification systems. With their help, customers can track their shipments in real time and plan their time to meet accurate delivery windows. Some logistics providers offer “safe drop” options, where customers can specify a secure location to leave the package if they are unavailable.
We also recommend providing customers with flexible delivery options, such as evening or weekend deliveries, catering to customers with busy daytime schedules. You could also request customers for alternative locations where they can pick up their shipments at their convenience, avoiding the need for reattempts.
6. Delays Caused by Unpredictable Events
Unpredictable events such as bad weather, road accidents, or natural disasters can disrupt last-mile delivery. These events are often beyond the control of logistics providers, yet can significantly delay shipments, causing frustration among customers and damaging the company’s reputation.
To mitigate the impact of such delays, companies can utilize real-time traffic monitoring and GPS systems to dynamically adjust routes when unforeseen events occur. Along with preparing backup routes and strategies for high-risk areas, they can help drivers avoid problem areas and ensure deliveries stay on track.
7. Return Deliveries
Nobody likes return deliveries, but sometimes they happen. Customers may reject shipments due to damage, poor quality, or incorrect orders. If so, handling returns can double the delivery cost. Furthermore, damaged or defective goods can lead to customer dissatisfaction and harm the company’s reputation if not managed properly.
To avoid product returns, companies should focus on improving the accuracy and quality control processes in their operations. Using better packaging materials can prevent damage during transit, while thorough quality checks ensure that only products meeting standards are shipped.
For handling returns more efficiently, logistics providers should also streamline reverse logistics processes. Dedicated teams or systems for returns management help minimize delays for the customer and the company, saving both money and reputation in the long run.